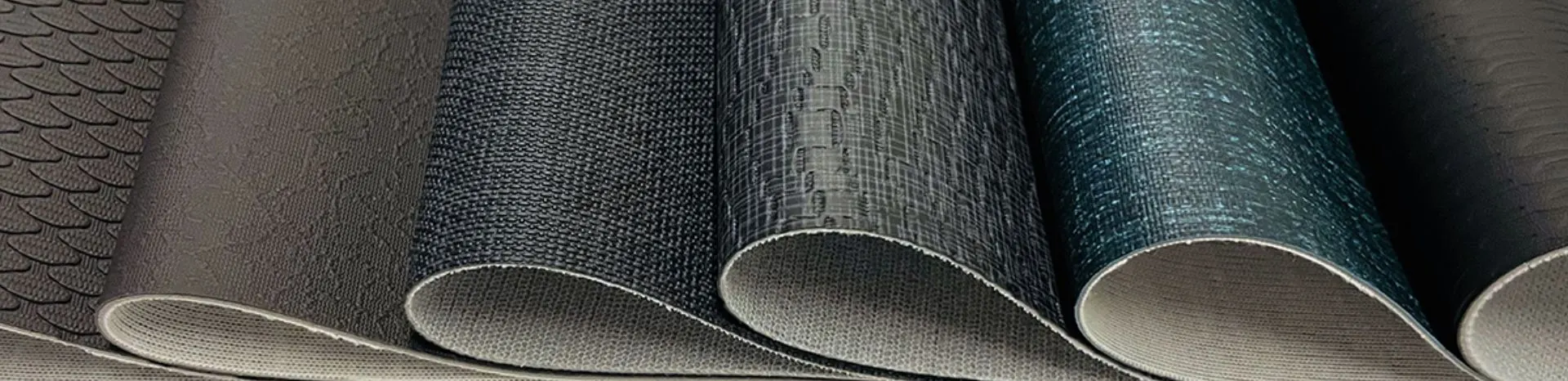
Automotive Solutions
Technical Support
Avoiding Discoloring of PVC Automotive Coverstock Materials
Pinking, yellowing, discoloring, and gas fading are adjectives used to describe color changes in PVC coverstock materials for automotive interior applications. This discoloring behavior has perplexed the automotive industry for more than decades, but there is no single supplier’s solution as it has been attributed by many different factors, less due to the formulation and product quality of vinyl material itself but more due to the lamination of PVC with polyurethane foams and the environmental storage conditions of the laminated goods. Fortunately, this discoloring phenomenon is strictly cosmetic and does not adversely affect the physical properties of the coverstock material. Moreover, the chemical reaction involved is reversible and thus the pinking can be eliminated with changes in the environmental or exposure conditions (such as UV sunlight).
Mechanism
It is important to recognize the fact that the discoloring issue can occur on the surface of not only PVC but also many different plastics such as polyolefin (PE/PP) and other polymeric materials. It is widely accepted in the industry that the over-oxidation of phenolic antioxidants contributes most significantly the discoloration. Although not being in CGT’s PVC formulation, phenolic antioxidants are used extensively in automotive polymers to provide heat and UV stability, for example, in polyurethane foams with which the PVC coverstock material is laminated. It is not possible or practical to eliminate the use of these additives. Oxidation of phenolic antioxidants in the PUR foam (such as BHT) can occur immediately during the lamination process, and the flame lamination process also provides vaporized channels to migrate the traces of the phenolic antioxidants and other contributing additives (such as amines) onto the vinyl surface. Phenolic antioxidants on the coverstock surface will be further oxidized via a reaction with atmospheric pollutants (mainly nitrogen oxides, NOx) to form to nitrated phenolic compounds (often called as “quinones”). Quinones containing phenolic hydroxyl groups are colored, varying from yellow to pink depending on the content of phenolic hydroxyl groups. Pinking or yellowing often forms during storage over days or weeks if the quinone has a high phenolic content, especially in a basic or alkaline environment when the surface pH value is higher than 7. Nitrogen oxides (NOx) are combustion products which can be found in poorly ventilated areas that use diesel gas/propane powered appliances/equipment (i.e., forklift trucks), cigarette smoke, space heaters or anything else that produces fossil fuel exhaust. These conditions are very typical in production plant environments or closed storage areas, especially during a shutdown and winter period, and can be greatly reduced by making sure the ventilation and air flow is adequate.
Factors
Several key factors will affect the pinking discoloration of PVC automotive coverstock materials:
- PVC raw materials: discoloring often occurs with white or light color PVC coverstock materials which use titanium dioxide TiO2 pigments. The quality and concentration of TiO2 used in a PVC formulation is more critical than any other raw materials used on the vinyl’s sensitivity to pinking or yellowing. At CGT, we ensure the grade and quantity of the TiO2 used in our PVC formulation are of the highest automotive quality which will not contribute to the discoloring issue. As for phenolic antioxidant, CGT does not add any to our vinyl formulation.
- Non-vinyl components such as PUR foam/adhesives and the lamination process: PUR foam/adhesives quality (with BHT or amine antioxidants) and lamination process (excessive burning and poor ventilation) will accelerate the migration of phenolic antioxidants on the vinyl surface.
- Atmospheric pollutants (NOx): NOx consist mainly of nitric oxide (NO) and nitrogen dioxide (NO2). Nitrogen oxide is readily converted to nitrogen dioxide in air. NO2 is a strong oxide which can promote the oxidation of phenolic antioxidants and generate colored species even at very low concentrations. NO2 concentrations in winter often exceed summer levels by 1.5-2 times with increased use of heating, lower ventilation rates, and higher outdoor concentrations.
Avoiding Discoloring of PVC Automotive Coverstock Materials
- Storage conditions: The age of the laminated vinyl, the amount of exposure to direct sunlight and subsequent ultraviolet rays, the heat and humidity conditions where the laminated vinyl is stored, the ventilation of the warehouse especially in winter months, the level of usage of gas-powered forklift trucks and/or oil or gas fired heaters, and whether the storage area has a high concentration of vehicle exhaust gases not exposed to sunlight are all key contributors to the discoloring issue.
- Surface condition of vinyl: Other surface actors that can aggravate the discoloring reaction are darkness, moisture and alkalinity, or compounds which have high pH. The higher the pH, the greater the tendency to see phenolic discoloration, especially “pinking”. Contaminating the warehouse atmosphere and the surface of the finished goods with QUAT (Quaternary Ammonium Compounds, pH>7.5) or other alkaline disinfectant/cleaning solutions could be more than normal due to the COVID-19 pandemic.
Possible Prevention and Mitigation
- General: There is no such thing of “super vinyl” which will never exhibit pinking, regardless of what non-vinyl components (foam and adhesives) are being used to make the soft trim parts for automotive interior coverstock applications and what storage conditions of the soft trim parts are stored. The only way to prevent the possibility of pinking or gas fading is to remove one of the two required components – either eliminate phenolic antioxidants or eliminate nitrogen oxides.
- PUR foam and Lamination process: Use high grade polyurethane foams without a phenolic antioxidant (BHT particularly), or with a phenolic antioxidant which is less prone to discolor, or with a non-phenolic secondary antioxidant (for example a phosphate) to alleviate the workload on the primary phenolic antioxidant. Avoid, if possible, the flame lamination process (for example, using adhesives) to make the soft trim material. Improve the flame lamination process parameters (such as better ventilation and burning control) which can effectively eliminate the migration of phenolic antioxidants and other trace chemicals to the vinyl surface and thus the subsequent discoloration phenomenon.
- Packaging: Pack the finished vinyl parts in plastic bags or polywraps, in order to prevent any deposition of trace chemicals and the interaction with NOx in the atmosphere. Avoid the contact of vinyl surface with lignin/cardboard which might contain other type of phenols.
- Storage: Ensure adequate ventilation is in place to allow for air circulation. Use slightly acidic cleaning solutions in the plant (pH around 5). Do not store parts in shipping containers for long period of time (>14 days). Control the fossil fuel combustion sources and/or provide adequate ventilation in these areas. Store parts in lighted areas, especially over a prolonged shut down.
- Mitigation: To reverse the discoloration reaction of the affected parts, expose them to